Optimizing Asset Tagging & Management with Service Automation
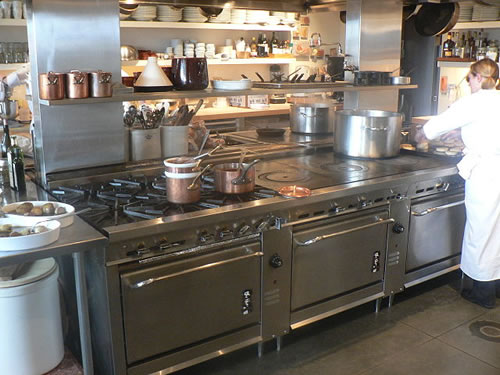
This is the first in a series of posts highlighting the importance of modern asset management for multi-location enterprises and how to take advantage of advancements like the latest in asset tagging technologies.
It’s safe to say that the history of asset tagging and tracking likely goes back to when the idea of developing and managing supply chains and procurement became important. In other words, humans have been tagging and tracking their assets for centuries, if not millennia. What has changed over those hundreds to thousands of years is the use of increasingly better technologies, most recently digital, to make the tagging and tracking of assets easier and more automated.
It may be surprising to know that some of the most important digital asset tagging and tracking technologies have had very long histories themselves. For example, RFID (radio frequency identification) goes back to the 1940s as an invention with mass commercialization taking hold in the 1980s.
The ubiquitous barcode goes back even further, to the 1930s as a concept and the 1970s for mass commercialization. Even NFC (near field communication), which is becoming so vogue now for mobile payment systems as well as modern asset tagging/tracking, has been around in silicon form since 2002, as a natural evolution to RFID.
So What’s New in Asset Management?
While these asset tagging/tracking technologies have proven themselves to be indispensable for the advancement of commerce, they have largely been discrete and independent elements unto themselves. Indeed, there are no shortages of asset tagging/tracking software and hardware options available, all promising to make life easier for users throughout the full lifecycle of their assets.
The discrete nature of these asset management systems can add to a company’s operational complexity in that their processes and data are not integrated into the larger workflow in any meaningful way. This can lead to “yet another system” for the business to manage, which tends to increase operational costs over time.
A New Approach: Service Automation Integration
But what if the process and output of asset tagging/tracking can be integrated into a larger workflow automation (process automation) layer of the business operations? Doing so promises users the ability to gain holistic visibility into assets they have in any of their locations and better understand the costs associated with repair and maintenance of these assets from a real-time and historical standpoint.
This is possible today by integrating asset tagging, tracking and management as yet another function of service automation, or the automation of events, processes and tasks through a unified interface or platform.
Further, we believe the most logical way to maximize the value of combining service automation with asset tagging, tracking and management is by incorporating these capabilities as a facilities management function.
The Case for FM-Led Asset Tagging, Tracking & Management
By the virtue of being whom we are and what we do, ServiceChannel has the privilege of working with tens of thousands of FMs in some of the largest, most influential companies in retail, restaurants, healthcare, grocery, public storage and many other vertical industries in the world today. Many of these companies operate highly distributed enterprises, often global in scale, with hundreds if not thousands of locations to manage on daily basis.
We know that many of these FMs are responsible for monitoring and maintaining the strategic assets at those locations in addition to the overall upkeep of the facilities. This makes a lot of sense.
For example, equipment failure at a restaurant (e.g. commercial refrigerators, stoves, etc.) might shut that location down until the issues are resolved. Or, the failure of a supermarket’s freezer cases will impact revenue and lead to costly food loss. Thus, the health of the critical assets at a facility is arguably as vital as the state of the facility itself.
Modern FMs are already using service automation as their work order management system including automating facilities repair and maintenance service requests. Combining service automation with asset tagging, tracking and management gives these FMs another important data stack that they can use to streamline operations, cut costs and make data-driven “repair or replace” decisions in real-time. In time, these FMs can build a powerful catalog of digital asset inventories, giving them benefits such as:
- Easier monitoring of assets as they’re moved between locations
- Warranty tracking and alerts to reduce or eliminate “warranty leakage,” for cost savings
- Utilizing preventive maintenance to minimize problems before they become big and costly
- Analyzing and reporting asset management data as part of a comprehensive FM analytics program
Innovating Asset Management
Helping our customers achieve these benefits was the primary motivation behind ServiceChannel evolving our existing Asset Manager product with the latest tagging and tracking capabilities.
Our customers already manage hundreds of thousands of critical assets through our platform. Giving them the ability to quickly tag, catalog and continually track existing and new assets is another step toward the vision of fully self-managing facilities.
Request a demo of ServiceChannel’s asset tagging, tracking, and management capabilities today.
This is part one of a series of blog posts on FM-led asset tagging, tracking and management. In the next post, we’ll look at some real-world use cases and scenarios of service automation-enabled asset management.
Photo: By Stuart Spivack; https://www.flickr.com/photos/stuart_spivack/ [CC BY-SA 2.0 (https://creativecommons.org/licenses/by-sa/2.0)], via Wikimedia Commons