How to Create a Preventive Maintenance Schedule in 6 Steps

A preventive maintenance schedule allows businesses to plan for the organization of resources to make sure their maintenance objectives and tasks are performed according to time and usage. This helps keep assets in working condition without lags in productivity.
Preventive maintenance is important because it keeps equipment and other assets efficiently operating, enhances safety for employees, and avoids excessive costs for repairs. Additionally, they correlate to a longer asset life, fewer disruptions to critical operations, improved efficiency, and less downtime.
What Is A Preventive Maintenance Schedule
A preventive maintenance (PM) schedule is a proactive plan that outlines specific maintenance tasks to be performed on your facility’s assets at predetermined intervals. These intervals can be based on time (e.g., monthly, quarterly, annually) or usage (e.g., operating hours, mileage). A well-structured PM schedule serves as your facility’s roadmap to consistent upkeep, ensuring that equipment remains in optimal working condition.
This systematic approach ensures that minor issues are addressed promptly, preventing them from escalating into major malfunctions or breakdowns. By adhering to a PM schedule, you can maintain the smooth operation of your facility and avoid unexpected and costly repairs.
Why is a Preventive Maintenance Schedule Important?
Preventive maintenance schedules are essential for ensuring the smooth operation and longevity of your facility’s assets. By proactively addressing minor issues before they escalate, you can reduce the risk of costly breakdowns and unexpected downtime. Regular maintenance not only extends the lifespan of your valuable equipment but optimizes its performance, leading to increased energy efficiency and lower operating costs.
Additionally, a well-maintained facility is a safer facility, as potential hazards are identified and mitigated through routine inspections and upkeep. A preventive maintenance schedule is a strategic investment that delivers tangible returns in terms of cost savings, enhanced reliability, improved safety, and increased operational efficiency.
Types of Preventive Maintenance Schedules
The ideal preventive maintenance plan for your business depends on your specific equipment, the criticality of various assets, and the resources available to your maintenance team. Here are some common preventive maintenance schedule types:
- Time-Based Maintenance (TPM): Routine maintenance tasks are performed at set intervals (monthly, quarterly, annually, etc.), regardless of equipment usage. TPM is suitable when assets require regular upkeep regardless of their operational intensity.
- Reliability-Centered Maintenance (RCM): This approach tailors maintenance strategies to the specific needs and criticality of each asset. RCM focuses on maximizing reliability and safety by identifying the most effective maintenance actions for each piece of equipment.
- Usage-Based Maintenance: Maintenance tasks are triggered by the actual usage of an asset (hours of operation, mileage, cycles). This is ideal for equipment with varying usage patterns, ensuring maintenance aligns with wear and tear.
- Condition-Based Maintenance (CBM): Sensors and data analysis monitor asset conditions, enabling early detection of potential failures. CBM allows for targeted interventions, reducing unnecessary maintenance and optimizing asset availability.
- Predictive Maintenance: Advanced analytics and machine learning predict failures based on real-time and historical data. This approach optimizes maintenance activities for critical assets, minimizing downtime and costly repairs.
- Planned Maintenance: Maintenance activities are scheduled during planned downtime or low-demand periods. This minimizes disruptions and maximizes resource utilization, especially for time-sensitive operations.
By understanding these different approaches, you can select the preventive maintenance schedule that best aligns with your organization’s goals and resources. The most effective strategy often involves a combination of these approaches, tailored to your unique operational needs.
How to Create a Preventive Maintenance Schedule
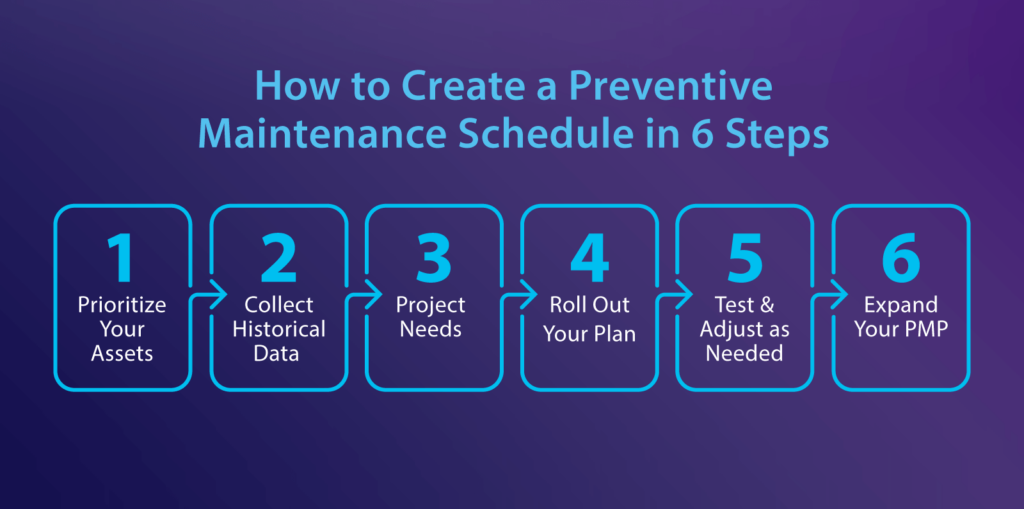
Even if your facility only has a few pieces of equipment, it can be challenging keeping up with everything. Making sure your equipment is in top condition and regularly monitored for wear and tear makes a difference. A preventive maintenance checklist is one of the best ways to achieve a productive and efficient maintenance schedule. Here’s how to get started with a preventive maintenance schedule for your facilities:
Step 1: Take Inventory & Prioritize Your Assets
To construct a good preventive maintenance program, you must know your assets and be proactive in having the right resources available. The goal is to prevent breakdowns before they happen to prevent reactive solutions that could cost the company more money. These assets should be prioritized based on the items that are most critical.
Once those assets are on a viable PM schedule, the other assets should fall in line based on the order of importance, their functions, costs to repair or replace, and those that are slated to be on their last leg. The objective is to have this in place to alleviate higher costs for breakdowns that could have been prevented.
Step 2: Collect Historical Data
A preventive maintenance scheduling template won’t work if you don’t have historical data on each asset. Everything should be listed, including when the asset was purchased, the maintenance performed on it, the types of problems that resulted in downtime, the age, the rate of depreciation, and any additional information that may prove helpful.
If you have a program that already keeps track of this information, you have a few steps already outlined for you. If not, it’s time to create a spreadsheet that keeps things organized and ready at a moment’s notice.
Step 3: Project the Needs of Your Assets
Based on how your assets have performed and the manufacturer’s recommendations, you should be able to assess how a recurring maintenance schedule will look. This is the time to speak to any technicians that work with the assets and figure out where the glitches in the current system are, and situations that aren’t mentioned by the manufacturer.
One of the best ways to understand your needs is by looking at what’s happened with the assets since being in use. Your technicians will be able to let you know if they have difficulty finding parts, how often the system breaks down, and what they do when downtime is an issue.
Step 4: Roll Out Your Plan
Now’s the time to put words and figures into action. Your plan should have a list of maintenance tasks for each asset and the timelines to follow for routine maintenance, notifications when the asset is having problems, and, of course, downtime. Not only will this help put things in perspective, but it can also be a baseline for how frequent your maintenance inspections should be.
Step 5: Test & Adjust Your Schedule as Needed
Practice makes perfect, so there may be a few rounds of inspections and monitoring of the workflow to see what needs tweaking. This is a process, so it’s natural to have to adjust some things as you go along. It’s also important not to schedule too much preventative maintenance, especially for those assets that really don’t require it.
Having a system in place that automates everything may be the right way to go. Not only does this prevent human error, but you’ll be able to see everything from a bird’s eye view to determine whether a certain asset doesn’t have enough maintenance scheduled. When assets break down, it’s important to see where they broke down and what is needed to repair them. In many cases, the entire machine isn’t at fault. It may be one specific reason. When this occurs, it would be too costly to service the entire machine. Your schedule can be adjusted to input that information.
Step 6: Expand Your Preventive Maintenance Program
Adopting a system to handle your preventive maintenance program will provide insight into how to use the software to optimize your schedule. Once implemented, cost savings and more efficiency should be realized very quickly. Once you are comfortable with how the system works, you can repeat the steps and expand your program throughout the company.
While the system may initially require a lot of manpower and data entry, the benefits gained from having an automated preventive maintenance program in place outweigh the cons. There are also programs that work with Excel or other software where the data can be migrated without too much interference.
Ready to Kickstart Your Maintenance Program?
Implementing a well-structured preventive maintenance schedule is a game-changer for any facility. It’s your roadmap to optimized asset performance, reduced downtime, and significant cost savings over time. But managing this process manually can be complex and time-consuming.
ServiceChannel’s preventive maintenance software simplifies the entire process, from scheduling tasks and tracking asset history to generating insightful reports. With our user-friendly interface and powerful features, you can streamline your maintenance operations, improve efficiency, and extend the lifespan of your valuable assets.
Don’t leave your maintenance program to chance and take a proactive approach. Explore our preventive maintenance software and discover how we can help you unlock the full potential of your facilities!